When it comes to commercial roofing, the thickness of the material plays a crucial role in its performance and longevity.
Understanding the appropriate thickness for different types of roofing material can help you make informed decisions that add value to your investment. Let us have it with Charles Jimerson from CJ Commercial Roofing NJ.
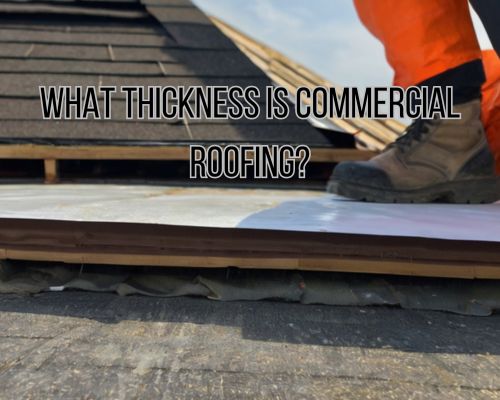
Commercial roofing thickness typically ranges from 0.032 inches for aluminum to more robust options like 0.050 inches, ensuring durability and resilience.
Selecting the right thickness is essential in maintaining the balance between weight and strength, impacting not only the durability but also the energy efficiency of your building.
Thicker materials like built-up roofing (BUR) systems, which consist of multiple layers of bitumen, offer excellent durability and long-term performance.
Whether you are looking at cost considerations or the specific structural needs of your building, it’s critical to understand how the thickness of your commercial roofing materials will affect its overall performance and value.
Fundamentals of Commercial Roofing Materials
Commercial roofing materials vary significantly in terms of type, thickness, performance, and price.
Each material offers unique benefits and considerations regarding durability, insulation, and overall suitability for different environments.
Material Types and Their Characteristics
Metal Roofing: Metal roofs, such as copper, galvanized steel, aluminum, and stainless steel, are prized for their longevity and resilience.
Standing seam metal roofs are popular in commercial applications due to their durability and low maintenance needs.
Single-Ply Membranes: Materials like TPO and EPDM are commonly used due to their flexibility and ability to withstand thermal expansion and contraction. These membranes also offer excellent waterproofing qualities.
Built-Up Roofing (BUR): This system involves multiple layers of bitumen and reinforcing fabrics, providing a robust and long-lasting roof. It is well-suited for flat and low-slope roofs.
Modified Bitumen: Similar to BUR but with added polyester or fiberglass for increased strength, this material provides enhanced durability and weather resistance.
Assessing Thickness and Its Impact on Performance
Thickness plays a crucial role in the performance and longevity of commercial roofing materials.
For metal roofing, the thickness can range from .032 to .050 inches, with thicker metals generally offering better durability.
Single-Ply Membranes: TPO and EPDM membranes’ thicknesses typically range from 45 mils to 80 mils. Thicker membranes generally provide enhanced resistance to punctures and other physical damage.
Built-Up Roofing: The thickness of BUR systems can vary based on the number of layers applied. Generally, more layers equate to a thicker, more protective barrier against moisture and weathering.
Importance of Thickness: Increased thickness often means better insulation and weight distribution.
Thicker materials tend to be more resistant to environmental stressors, contributing to longer-lasting roofs.
Design and Application Considerations
When designing commercial roofing, various factors must be taken into account, including color selection, architectural customization, and the integration of insulation during installation. These considerations ensure the roof meets functional, aesthetic, and safety requirements. Let us dig more with Charles Jimerson from CJ Commercial Roofing NJ.
Commercial Roof Color Selection
Color selection is crucial for both aesthetics and energy efficiency.
Lighter colors like white or reflective coatings can reduce cooling costs by reflecting solar radiation. Meanwhile, dark colors such as black absorb heat, which may be beneficial in colder climates.
The choice of color also affects the building’s architectural harmony. Regulatory guidelines often dictate specific color requirements to enhance urban heat management. Always consult local building codes and environmental regulations before finalizing the color.
Customization for Architectural Needs
Commercial roofing can be tailored to fit unique architectural styles.
Architects may require the use of specific materials or design elements to achieve a certain look.
Customization might involve choosing specific types of insulation, adhesives, or accessories to meet design goals.
For example, metal roofs offer flexible design options but require appropriate customization for durability. Complex designs may also involve additional safety measures and compliance checks.
Installation Techniques and Insulation Integration
The choice of installation technique impacts the roof’s performance and longevity. Adhered systems offer seamless finishes. Meanwhile, mechanically fastened options provide robustness against high winds.
Proper integration of insulation is essential. Insulation not only aids in thermal regulation but also contributes to the structural integrity of the roof. Materials like foam board or sprayed polyurethane foam are commonly used.
Ensure insulation materials meet the specific thermal and moisture control specifications for your project.
Effective installation practices and thorough inspection protocols are critical. Safety measures should always be a priority during any installation process to prevent accidents and ensure long-term performance.